

General tensile mechanical property profiles are presented for a variety of PFRPs to enable the design for i) optimal stiffness and strength, ii) minimal weight (i.e. To aid design engineers in closing the existing gap between current scientific knowledge and actual market applications of plant fibre reinforced plastics (PFRPs), this article provides comprehensive Ashby-type materials selection charts for PFRPs to facilitate product design and development. Overall, our results suggest that our model could be used to help design better thermal sensors for robots and enable robots to use them more effectively. Using our model, we also provide insight into the roles of various factors on recognition performance, such as the temperature difference between the sensor and the object. Our model predicted the material recognition performance of support vector machine (SVM) with 96% accuracy for the simulated data, with 92% accuracy for real-world data with constant initial sensor temperatures, and with 91% accuracy for real-world data with varied initial sensor temperatures. We evaluated our method using simulated contact with 69 materials and data collected by a real robot with 12 materials. Our model uses semi-infinite solids and a statistical method to calculate an F1 score for the binary material recognition. We present a physics-based mathematical model that predicts material recognition performance given these factors. While data-driven methods have shown promise for this recognition problem, many factors can influence performance, including sensor noise, the initial temperatures of the sensor and the object, the thermal effusivities of the materials, and the duration of contact.
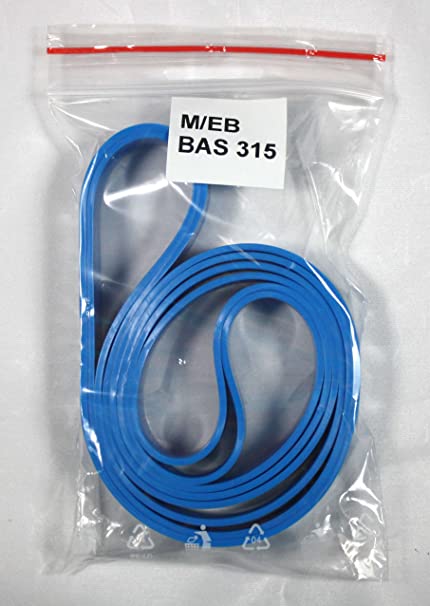
Heat transfer based sensing can be used for material recognition due to differences in the thermal properties of materials. Tactile sensing can enable a robot to infer properties of its surroundings, such as the material of an object.
